EHS Software for Operations & Safety: Boost Compliance & Cut Risk
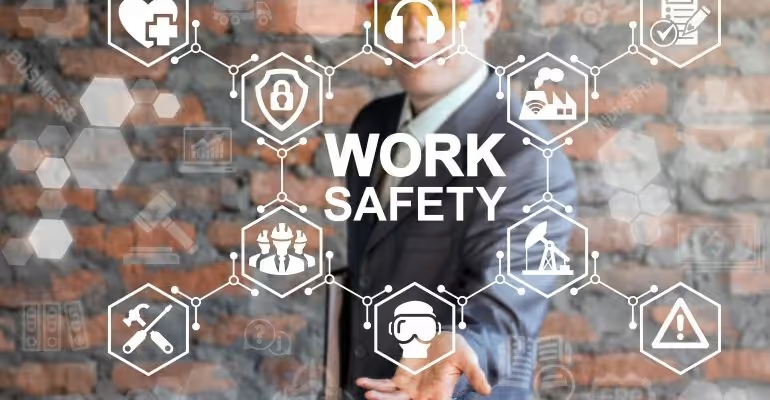
Managing workplace safety and compliance in the U.S. has never been more complex. With stricter OSHA and EPA regulations, companies are under constant pressure to protect employees, reduce risks, and document compliance. That’s where an EHS Management System comes in, a centralized solution that combines safety, health, and environmental management into one framework. In this blog, we’ll break down how EHS systems work, why they matter for U.S. businesses, and what features you should look for when adopting one.
What is an EHS Management System?
An EHS Management System is a structured framework that helps organizations manage environmental, health, and safety (EHS) compliance. It streamlines workplace safety, regulatory reporting (like OSHA/EPA in the U.S.), risk management, and sustainability goals through policies, processes, and software tools that ensure safer, compliant operations.

Why U.S. Businesses Need EHS Management Systems
U.S. businesses should implement an effective Environmental, Health, and Safety (EHS) management system to proactively manage risks, ensure regulatory compliance, and protect their workforce. An EHS system provides a structured framework for organizations to identify and control hazards, minimize incidents, and continuously improve their environmental and safety performance.
Beyond a legal obligation, a robust EHS program is a strategic investment that can significantly impact a company's financial health, public image, and operational efficiency.
OSHA & EPA Compliance
- Staying compliant with regulations from agencies like the Occupational Safety and Health Administration (OSHA) and the Environmental Protection Agency (EPA) is a primary reason for EHS systems. These systems provide a structured way to track and meet all legal requirements.
- An EHS management system helps businesses avoid costly fines and legal penalties associated with non-compliance. It creates a centralized record of training, inspections, and permits, making it easier to demonstrate due diligence during audits.
- By systematizing compliance efforts, companies can move beyond reactive, fire-fighting mode and adopt a proactive approach. This ensures all new regulations are incorporated into business operations as they are released.
Risk Reduction & Employee Safety
- EHS management systems are designed to identify and assess workplace hazards before they cause an incident. This proactive approach helps reduce the frequency and severity of injuries, illnesses, and environmental releases.
- Protecting employees is a core function of any EHS system. It establishes clear safety protocols, provides necessary personal protective equipment (PPE), and ensures all workers receive proper training on how to perform their jobs safely.
- A strong safety culture, fostered by an EHS system, improves employee morale and productivity. When employees feel that their employer genuinely cares about their well-being, they are more likely to be engaged and committed to their work.
Financial & Reputational Impact
- Implementing an EHS system can lead to significant financial savings. By preventing incidents, businesses can reduce costs related to medical expenses, workers' compensation claims, and lost productivity from missed workdays.
- A company with a good safety record and strong environmental stewardship builds a positive reputation among customers, investors, and the community. This can lead to new business opportunities and increased brand loyalty.
- The system's focus on efficiency and waste reduction can also lead to cost savings. For example, optimizing processes to reduce material waste or energy consumption directly benefits the company's bottom line.
Key Features of an Effective EHS Management System
Incident Management
- An effective system allows for the swift and accurate reporting of all incidents, including near misses, injuries, and environmental spills. This feature is crucial for capturing data at the source.
- It provides a structured process for conducting thorough root-cause analysis to determine why an incident occurred, rather than just treating the symptoms.
- The system facilitates the implementation and tracking of corrective and preventive actions to ensure similar incidents don't happen again. It ensures accountability and a clear trail of follow-up.
Compliance Tracking
- This feature centralizes and organizes all relevant EHS regulations, permits, and standards that apply to the organization, making it easy to access and understand compliance obligations.
- It provides proactive alerts and notifications for upcoming deadlines, permit renewals, or changes in regulations, helping to prevent non-compliance issues before they arise.
- The system offers a clear overview of compliance status across different sites or departments, allowing management to quickly identify and address areas of non-conformance.
Audit Management
- An EHS management system streamlines the planning and scheduling of internal and external audits, ensuring that all required checks are performed on time.
- It offers a standardized way to conduct audits using customizable checklists and forms, which helps maintain consistency and accuracy across different assessments.
- The system centralizes audit findings, tracks the progress of corrective actions, and provides a clear record of the organization's efforts to address non-compliance and drive continuous improvement.
Training & Reporting
- This feature helps organizations manage a comprehensive training program, including assigning mandatory courses, tracking employee completion, and storing training records.
- It provides tools to generate detailed reports and dashboards on key EHS metrics, such as incident rates, training compliance, and audit findings.
- The system enables data-driven decision-making by offering insights into performance trends and identifying high-risk areas, allowing management to allocate resources effectively.
Benefits of EHS Management Systems for U.S
Improved Compliance Efficiency
- EHS management systems create a centralized hub for all compliance-related documentation, including permits, licenses, and inspection reports. This makes it much easier for companies to track and manage their regulatory obligations.
- Automated alerts and task reminders within the system help ensure that all required deadlines are met, reducing the risk of costly fines and penalties for non-compliance.
- By standardizing EHS processes and procedures across the organization, companies can conduct internal audits more efficiently and prepare for external regulatory inspections with greater confidence. This systematic approach streamlines compliance activities and reduces administrative burden.
Reduced Workplace Incidents
- EHS systems facilitate proactive risk management by enabling companies to identify and assess potential hazards before they lead to an incident. This includes analyzing trends in near-misses and minor incidents to prevent more serious accidents.
- These systems provide tools for comprehensive incident reporting and investigation, allowing companies to understand the root causes of accidents and implement effective corrective actions.
- By tracking and managing employee training and certifications, EHS software ensures that all workers have the necessary knowledge and skills to perform their jobs safely, fostering a strong culture of safety.
Stronger Sustainability Initiatives
- EHS management systems help companies track and report on their environmental performance, including energy consumption, water usage, and waste generation. This data is essential for setting and achieving sustainability goals.
- They provide a framework for developing and implementing environmental programs, such as waste reduction strategies or energy efficiency projects. These initiatives can lead to operational cost savings in the long run.
- By transparently managing their environmental impact, companies can enhance their brand reputation and demonstrate a commitment to corporate social responsibility, which is increasingly important to consumers and investors.
Best Practices for Implementing EHS Management Systems in the USA

Aligning with OSHA and EPA Standards
- Conduct a thorough gap analysis to compare your current EHS practices against OSHA and EPA regulations. This helps identify areas where you need to improve to achieve full compliance.
- Develop a written EHS policy that clearly states your company's commitment to safety and environmental protection. Ensure this policy is communicated to all employees and is easily accessible.
- Establish a clear chain of command for EHS responsibilities. Designate specific individuals or teams to oversee compliance, conduct inspections, and respond to incidents.
- Implement a robust hazard identification process including regular workplace inspections, job hazard analyses, and incident investigations. This proactive approach helps prevent accidents before they occur.
Training Employees
- Provide comprehensive initial and ongoing training on EHS policies, procedures, and specific job-related hazards. Training should cover topics such as emergency response, proper use of personal protective equipment (PPE), and safe handling of hazardous materials.
- Make training interactive and relevant to employees' daily tasks. Use practical demonstrations, group discussions, and real-life scenarios to enhance understanding and retention.
- Document all training sessions, including dates, topics covered, and attendee lists. This documentation is essential for demonstrating compliance during audits and inspections.
- Encourage employee participation in safety committees and hazard reporting. Empowering employees to be active participants in the EHS program fosters a culture of shared responsibility.
Continuous Monitoring with Digital Tools
- Utilize EHS software platforms to streamline data collection, automate reporting, and centralize documentation. Digital tools can help manage everything from incident reports to training records and compliance checklists.
- Implement real-time monitoring devices for environmental factors like air quality and chemical spills. These tools provide immediate alerts, allowing for a swift response to potential hazards.
- Use mobile apps for conducting safety inspections and audits on-site. This allows for immediate data entry and photo capture, improving accuracy and efficiency.
- Leverage data analytics from your digital systems to identify trends in incidents or non-compliance. This data-driven approach helps you target specific areas for improvement and allocate resources effectively.
Case Study: EHS Implementation for a U.S. Manufacturing Firm
This case study highlights how a leading U.S. manufacturing firm, grappling with outdated safety management processes, transformed its environmental, health, and safety (EHS) operations. By digitizing its systems, the company not only improved safety and compliance but also gained valuable data to make proactive, informed decisions.
Problem
The manufacturing firm faced significant challenges with its manual EHS processes, which were time-consuming and inefficient.
The primary issues included:
- Manual Safety Scorecards: Calculating safety scores was a slow, error-prone manual process, making it difficult to get real-time insights into performance.
- Inefficient Incident Management: The company struggled with a slow and unstructured process for reporting and resolving safety incidents, which often led to delays and a lack of accountability.
- Paper-Based Audits: Maintaining inspection checklists on paper or in complex spreadsheets was a tedious and frustrating task that resulted in low completion rates and poor data quality.
- Poor Compliance: The manual, paper-based system led to a low overall compliance percentage, putting the company at risk and hindering its ability to ensure a consistently safe workplace.
Solution
To address these challenges, we developed and implemented a comprehensive digital application for the firm’s EHS needs. The solution was designed to streamline the entire safety audit and incident management lifecycle, from creation to resolution.
Key features of the application included:
- Centralized Audit Management: The platform allowed users to create, assign, and conduct dynamic safety audits on tablets, eliminating the need for paper. This ensured all audits were managed from a single, centralized system.
- Automated Scorecard Generation: The system automatically calculated safety scores in real-time based on audit inputs, providing an immediate and accurate overview of compliance without any manual effort.
- Structured Incident Workflow: The application established a clear, level-based approval workflow for reporting and escalating incidents. This structured process ensured that all incidents were managed efficiently and with full accountability.
Results
The implementation of the new digital EHS platform led to significant and measurable improvements across the firm's operations and safety performance.
- Compliance and Accountability: The company saw a 30% improvement in safety compliance and achieved 100% enhanced accountability and transparency in its safety processes.
- Operational Efficiency: The new system made safety audits 50% faster, streamlining workflows and freeing up valuable time for EHS staff to focus on proactive safety measures.
- Faster Incident Resolution: By implementing a structured incident management workflow, the firm reduced incident resolution time by 40%, ensuring a quicker response to safety issues and minimizing potential risks.
The digital solution transformed the firm's approach to safety, moving them from a reactive, manual system to a proactive, data-driven one. This shift not only improved key performance indicators but also fostered a culture of safety and accountability throughout the organization.
Future of EHS Management Systems in the U.S
The future of EHS (Environmental, Health, and Safety) management in the U.S. is being revolutionized by technology, moving from reactive compliance to proactive risk management.
This evolution is driven by the integration of sophisticated tools and data analysis, which are transforming how organizations approach safety and sustainability.
- AI-driven safety analytics are at the forefront of this transformation. Instead of simply recording incidents after they happen, these systems analyze vast amounts of data from sensors, incident reports, and even employee feedback. This allows them to identify patterns and root causes that human analysis might miss. For example, AI can predict high-risk areas on a factory floor or specific tasks likely to lead to injury, enabling targeted interventions and training before an incident occurs.
- Predictive compliance tools are also changing the game. These tools use machine learning to monitor regulatory updates and forecast how they will impact a company's operations. They can automatically identify which regulations apply to a specific facility, flag potential non-compliance issues, and suggest corrective actions. This helps companies stay ahead of new standards, reducing the risk of fines and legal issues while ensuring a consistent, high level of safety and environmental performance.
Why Modern EHS Software Is a Game-Changer
I’ve seen what happens when companies stick with outdated EHS processes, higher costs, more incidents, and stressed-out teams. But I’ve also seen the transformation when they adopt modern EHS management systems.
A manufacturing client reduced their incident rate by 30% and saved $200,000 annually in compliance penalties and lost productivity. Another healthcare provider improved audit performance, passing OSHA inspections with zero violations.
These systems don’t just solve problems, they give you a competitive edge by:
- Cutting incident rates and costs.
- Ensuring compliance with OSHA, EPA, and more.
- Boosting efficiency and freeing up your team.
- Building a stronger safety culture.
FAQs About EHS Management Systems
Q1. What does an EHS Management System include?
It includes tools for incident management, compliance tracking, audits, employee training, and environmental monitoring.
Q2. How does an EHS Management System help with OSHA compliance?
It automates compliance reporting, ensures regulatory alignment, and reduces the risk of penalties by tracking OSHA requirements.
Q3. Why should U.S. manufacturers use an EHS Management System?
Manufacturers face high safety risks and strict compliance requirements. EHS systems help reduce incidents, avoid fines, and improve safety culture.
Q4. What industries benefit most from EHS Management Systems?
Construction, manufacturing, oil & gas, logistics, and healthcare benefit the most due to their high regulatory demands.
Q5. Is EHS Management System software worth the investment?
Yes. It saves money by reducing accidents, ensuring compliance, and avoiding costly penalties.
Ready to Transform Your EHS Program?
The stakes are high, every day you stick with outdated systems, you’re risking fines, incidents, and lost productivity.
I’ve helped companies across the U.S. turn their EHS challenges into strengths with modern software.