How Connected Workforce Platform Improves Workforce Performance and Productivity
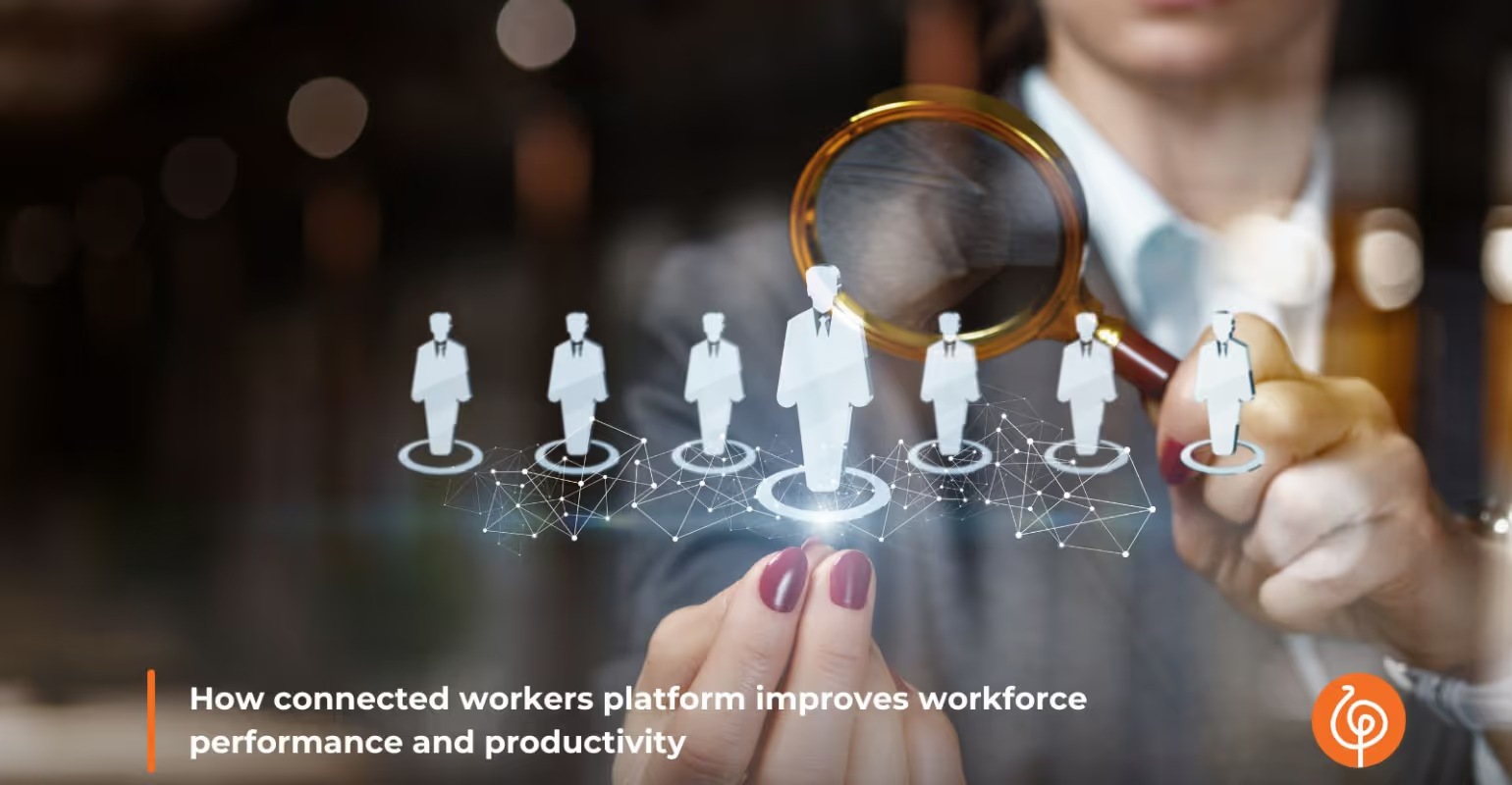
Reasons that affects Manufacturing Productivity
Here are some of the reasons that hamper manufacturing productivity and growth.
- Labor shortage,
- unskilled workers,
- lack of real-time performance tracking,
- manual job card assignments,
- difficulty in reaching production goals,
- irrelevant KPIs and monitoring,
- lack of communication among staff
- lack of communication between management and staff
- lack of technology and automation,
- lack of real-time data collection and analysis tools, and
- lack of data for management to make impactful decisions, etc.
All these factors associated with the Covid-19 impact have marred manufacturing productivity, performance, and growth.
The industry, reeling under pressure, is looking for advanced solutions and techniques to improve production quality, accelerate productivity, and elevate RoI.
With customer demand growing and gripping, industries must identify the gaps in the performance and production areas to ensure seamless and effective delivery of products to customers.
Here in this post, I will walk you through the challenge: lack of communication among employees and between employees-management. As this is one of the concerns that can improve production significantly, the post will detail why connecting employees with each other and the management team will improve productivity.
Is your organization left behind? It’s time to invest in new technologies to accelerate manufacturing efforts.
Technologies that are transforming the manufacturing employee performance
Here are some of the technologies that are transforming the manufacturing employee landscape and performance.
- Internet of things
- Artificial Intelligence
- Robotic Process Automation
- Cloud
With the help of technologies, manufacturing companies can bring down the cost of
- Manual paper works
- Telephone bills
- Equipment maintenance
- Inventory management
- Order and delivery tracking
If you carefully analyze the above cost challenges, you can witness that communication between management and laborers is a potential problem, leading to needless expenses.
Let’s see how a connected workforce platform can transform how management communicates with the workforce.
The need for a connected workforce platform
With the next wave of Covid-29 expected shortly, manufacturing companies must try new technologies that will help them reshape the way employees work and communication within manufacturing enterprises.
With obsolete and discreet technologies and solutions, it is hard to connect with remote workers and initiate communication among them. It requires a set of technologies, solutions, and apps to ensure seamless communication is orchestrated between an employee-employee and employee and management.
The significance of connected workforce platform
The good thing about a connected workforce platform is that it helps the workforce communicate better and ensures that production is carried out seamlessly. The process of assigning tasks, managing the workforce, sharing data, and updating data, is straightforward so that your management team doesn’t have to wait for a long time to make impactful decisions.
With technologies like IoT and AI, data collection from different points makes the workforce easy, and the management team can easily pull real-time data from the production floor. This reduces the time to collect and analyze data as AI does it in the Cloud platform after the IoT devices collect the data.
Key benefits of connected workforce platform
1. Assured safety
When you have the complete data shared between the staff and more intelligent technologies are in use, you don’t have to worry about workforce safety. Real-time data will ensure employees know the complete details about the faulty or malfunctioning machines and can easily stay away from them. With the help of technologies and apps, the workforce can enjoy a stress-free production arena, leading to accelerated productivity and performance.
READ MORE : 6 Challenges That Can Be Solved With The EHS Management System
2. Seamless communication
Real-time data acquired and shared between the employees and management ensures a seamless production workflow across the manufacturing floor. When you have painless communication among workers, then most often, the result would be an increase in productivity rate. As the workers don’t have to wait for data compared to manual processes, they can speed up the production rate significantly.
3. Improved productivity
Manufacturing is all about production and delivery. If you don’t a reliable system that contributes to productivity, then you’re gone. The connected workforce platform enables the staff to perform their day-to-day activities like assigning tasks, sharing data, tracking their goals, etc., without discomfort. In other words, it results in improved productivity.
Also, real-time data tracking ensures the workforce and management keep a tab on the KPIs set against each employee and their performance toward it every day. So the management, based on the performance, can adjust the goals and assign tasks so that the daily productivity rate is achieved without breaking a sweat.
4. Automated workflows
Connecting the processes and employees with technologies like IoT, AI and Cloud will help you automate the workflows and speed up daily tasks. Starting from data collection, processing, task assignments, decision-making, and inventory management, everything will be breezy with the help of technologies used for workflow automation.
Streamlining workflows and having accurate data from the processes will help the management to readjust or reinvent a few ideas that will materialize into improved benefits and contribute to higher RoI.
Conclusion
Today, manufacturing companies must develop new ideas and innovative measures to take their businesses to the next level.
With Covid-19 and labor shortage hurting the business progress and growth, it is high time for companies to invest in next-generation technologies like IoT, AI, Cloud, Mobile Apps, etc.
While a few companies consider cost as a significant concern for transiting to the new processes and technologies, it is always the benefits they must focus on. Also, the connected workforce platform enabled by futuristic technologies can ensure your business meets the growing demands on time and beats the competition without hassle.
So, are you ready for the change? If yes, wait no further. Start exploring the opportunities and talk to an expert today.
Have queries or need solutions? We’re all ears. Let’s talk.
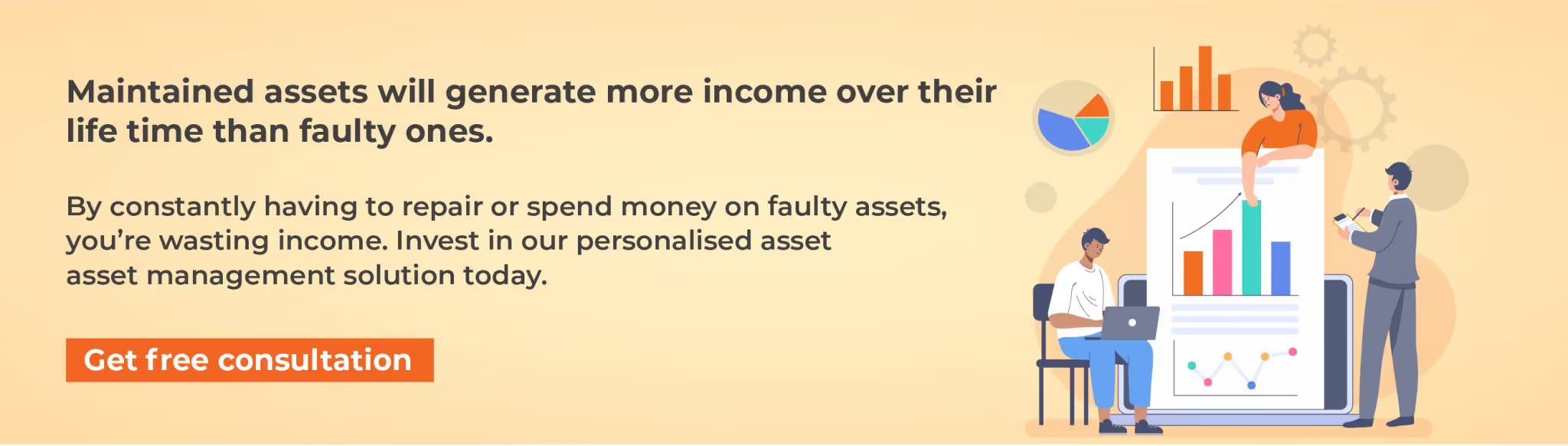