Predictive Maintenance for Manufacturing- Why It Matters and How It Works
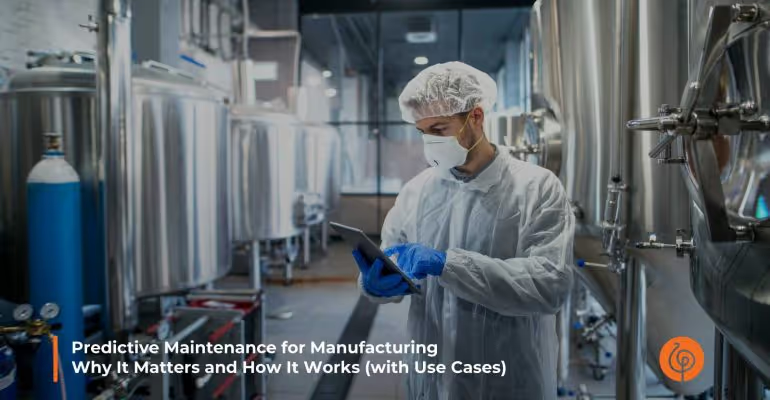
Predictive Maintenance- A Brief Introduction
Anyone who belongs to or hails from a manufacturing ecosystem will always vouch that there isn’t a single day in this field that doesn’t witness failures and breakdowns. As a field that deals exclusively with equipment and machinery programmed to carry out a repetitive task, the malfunction’s scope is inevitable. Thus, most manufacturing industries’ objective is not to eliminate this margin of error but to instead minimise it to such an extent that it helps them achieve high-efficiency standards and deliver quality products in the process.
Thanks to the rapid evolution of science and technology, companies no longer need to rely on rudimentary techniques such as importing data to spreadsheets and analysing insights manually to track the progress of their operations. With the rise of tools such as the Internet of Things and Big Data, they now have the liberty to leverage machine data to limit the costs and impacts of the odd downtime, irrespective of whether it is planned or unplanned. This protocol of crisis management is, in a nutshell, referred to as predictive maintenance.
Diving Further
In more technical terms, predictive maintenance refers to conducting maintenance in a bid to keep predicted problems at bay. It can be seen as a proactive method of foreseeing maintenance requirements on a factory floor and catering to it immediately, rather than sticking to the traditional way of ‘condition-based maintenance, which involves carrying out maintenance following a fixed schedule or only to combat a newly encountered issue. Predictive maintenance entails analysing operational data from machines, subsequently giving rise to a host of indicative patterns and insights. These patterns are then taken into account by operators, who utilise them to predict any given unit’s maintenance schedule within the system.
Before the advent of predictive maintenance, manufacturers had to rely on the reactive maintenance model wherein they proceeded with fixing a particular unit only after it became malfunction. With this model at the helm, not only did the manufacturing industry incur high maintenance costs but also found themselves paralysed by long stretches of unplanned downtime. All of these factors inevitably brought about a degradation in the quality of the output that was being produced. On the contrary, with IoT and IIoT (Industrial Internet of Things) integrated predictive maintenance models at their disposal, the industry could cut substantial costs by eliminating the need for unnecessary frequent maintenance. It is an extremely intuitive method that takes into account specific information extracted from each unit to detect and predict potential issues, thereby upholding the overall health of the manufacturing industry in the process.
ALSO READ: How to transform your Shop Floor with Industrial IoT?
Why is Predictive Maintenance Important?
In industries like manufacturing, where depreciation is a vital cost and advanced equipment is high-priced, ensuring sound asset management becomes rather critical towards ensuring the sustainability and the longevity of the manufacturing unit in question. Implementing the model of predictive maintenance in these setups allows one to save substantial costs at multiple ends. Even though there are protocols such as lean management and six sigma, whose sole purpose is to enhance a unit’s efficiency, their relevance comes under the scanner in the current scheme of things.
In a day and age where technology has come to dictate almost every tangible aspect of our lives, it has become imperative to have efficiency protocols in place that are tech-driven. In essence, thus, predictive maintenance presents itself as the newest level under the asset management methodology. According to a PwC report, implementing predictive manufacturing in maintenance reduced the costs by 12% and improved the uptime by a factor of 9%. Additionally, it was also seen to extend the lifetime of ageing assets by 20%, besides bringing down safety, environmental, quality, and health risks by as much as 14%.
How does Predictive Maintenance Work?
While the general construct of predictive maintenance is primarily intuitive, it takes into account a host of sensor data to monitor the machine’s condition at all times effectively. These sensors include:
- Pressure
- Rotation Speeds
- Temperature
- Current
- Vibration
- Chemical Properties Oil
Depending on the unit that is under consideration, the predictive maintenance model considers the readings generated by these sensors to predict potential hazards and subsequently issue maintenance work orders. Each of these sensors is responsible for monitoring a different aspect of the unit. Hence, the values of their readings are directly indicative of the state of the machinery in question. For instance, vibration analysis provides insights into possible breakdowns and may be treated as the early signs of an imminent component failure. Similarly, the temperature sensor’s high readings may indicate a particular component approaching a possible meltdown shortly. Usually, the protocol is invoked into action whenever the readings lie either below or above the designated average or ‘normal’ value.
Advantages of Predictive Maintenance
- Helps Optimise Planned Downtime- The aspects of machine cleaning, replacement of risk-prone parts, and oiling all fall under the broader umbrella of planned downtime. Integrating these practices with the intuitive and data-driven model of predictive maintenance allows for greater optimization and reduces the risk of unplanned downtime. Because predictive maintenance relies on the data collected from machine operations, it becomes substantially more convenient to schedule maintenance operations. Subsequently, this plays a pivotal role in extending the lifetime of ageing assets, ensuring that the production witnesses no significant breakdowns.
- Helps Limit Unplanned Downtime– Nothing plays as much of a role in causing a manufacturing unit’s ruin as that of unplanned downtime. According to a Wall Street Journal post, an estimated $50 billion is incurred by industrial manufacturers annually in unanticipated downtime costs. Thus, these units must limit unplanned downtime to a bare minimum. One of the best ways of accomplishing this objective is using predictive maintenance to have proactive maintenance schedules. Predictive maintenance takes into historical account data to detect patterns that help identify machines that stand the risk of experiencing an outage shortly.
- Helps Optimise Equipment Lifetime- By effectively eliminating the practices of scheduled maintenance and condition-based maintenance, predictive maintenance facilitates the optimisation of equipment lifetime by monitoring their output, efficiency, and quality at all times. Depending on their life and their frequency of usage, the model allocates different schedules to all the unit’s various operational components.
Predictive Maintenance Use Cases
- Connected Cars– The implementation of predictive maintenance in connected cars in the automotive industry is perhaps among the most compelling use cases of predictive maintenance out there. These connected cars create and relay a significant amount of performance data generated from all of its constituent sensors. Consequently, having predictive maintenance in place allows the dealership and the manufacturer to fix servicing and maintenance schedules for their customers, saving them the trouble of unforeseen inconveniences and enhancing their user experience in the process.
- Utility Suppliers- Utility suppliers these days are increasingly making use of predictive maintenance and analysis to detect early warning signs of supply and demand issues on the grid and subsequently address them before they escalate into potential outages.
- Research- Research giants like CERN use the large volumes of data generated by their millions of sensors to ensure that all of its equipment and machinery is operating at maximum potential. Subsequently, this also gives them the cushion of identifying and addressing potential malfunctions well in advance.
Hakuna Matata Tech to the Rescue
If you are looking to simplify your industrial operations and level shoulders with the other giants of the industry, you need to look no further. With our extensive suite of Industrial IoT solutions and digital transformation services at your disposal, we’ll not only help your industrial unit effectively transition into a predictive maintenance model but also help you save valuable time and money in the process.
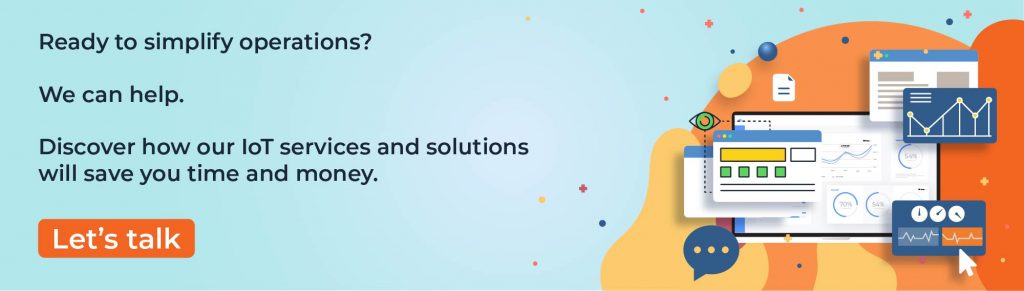