Why Smart Manufacturing is the need of the hour?
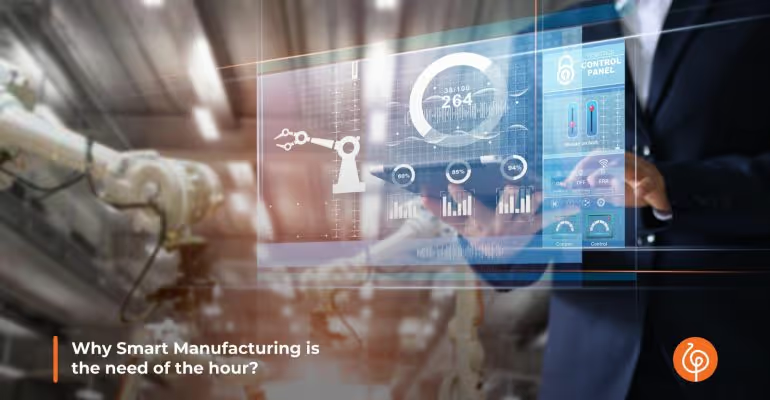
What is a smart factory?
A smart factory is quite simply a highly digitized shop floor that continuously collects and shares data through connected machines, devices, and production systems. The data can then be used by self-optimizing devices across the organization to proactively resolve issues, improve manufacturing processes and respond to evolving customer demands.
Several cutting-edge technologies work together in a symphony to create a smart factory including, Artificial Intelligence (AI), Big Data Analytics, Cloud Computing, and Industrial Internet of Things.
By integrating the physical and digital world, smart factories give you a clear picture of the entire production process, right from manufacturing tools and supply chain to individual operators on the shop floor. When utilized correctly, smart manufacturing renders operations flexible, adaptable, and optimizable.
Explore the technologies behind a Smart Factory
Industrial IoT (IIoT)
Industrial IoT refers to a system of interconnected devices, machines, and processes, which are linked by data communication systems to facilitate the exchange and use of data between people and machines.
Typically these instruments have sensors, which collect meaningful data on the cloud or an offline database. This data can be used to track and identify ways to improve manufacturing processes on the shop floor.
Sensors
Sensors attached to devices and machines collect and generate actionable data insights at different stages of the manufacturing process. For example, temperature sensors in a cleanroom can track and detect the climate in a lab and share that data through an IoT gateway.
This data can be used to alert team members for a review or self-correct using AI to resolve any deviations or anomalies.
Cloud Computing
Cloud computing allows factories to store, process, and share data with greater flexibility and at a lower cost than traditional on-premise alternatives.
Interconnected devices and machines on the shop floor are rendered more capable since cloud computing allows large amounts of data to be uploaded at record speeds.
Big Data Analytics
The accumulation of data over time can provide insights into how efficient the production process is, key metrics to track, and which systems are underperforming.
Big Data can spot error patterns and run predictive quality assurance with high accuracy.
Although smart manufacturing has lately been doing the rounds in manufacturing circles, a quick look at recent market conditions reveals that most manufacturers have made little progress in their journey towards digitizing the factory floor.
Many manufacturers were steeped into multimillion-dollar Industry 4.0 or IoT initiatives, but without any results to show for their efforts. Let’s explore why this is the case with some examples.
As coronavirus swept through the world, some manufacturers hastened to pivot and keep up with the changing market scenario. Ford Motor Company lent its manufacturing expertise to the medical industry to build lifesaving machines and equipment.
Bacardi manufactured hand sanitizer, and Purell dramatically increased production. Nike added face shields to its product line and Gucci made face masks.
On the other hand, many toilet paper companies, such as Angel Soft, couldn’t keep up with demand because their factories were already at 100% production during normal times.
The meat processing industry has been slow to embrace robotics, which likely added to its inability to adapt to coronavirus outbreaks and restrictions.
Witnessing a pattern here? During the coronavirus outbreak, an incredibly important business driver emerged on top of age-old manufacturing concerns like quality and operations: agility.
The winners were agile, they put large, and difficult-to-implement IoT initiatives on hold in favor of simple smart manufacturing solutions.
5 reasons why you should adopt smart manufacturing solutions
Smart manufacturing allows manufacturers to level up their game on three fronts: manufacturing agility, worker safety, and service continuity. Digging deeper, here are 5 ways in which smart manufacturing can help transform your business:
- Quick identification and resolution of bottlenecks: Collecting operational equipment data like cycle time, downtime and uptime allow manufacturers like you to paint a picture of what is happening on the shop floor so they can identify process bottlenecks and fix them.
- Improve operational performance: Real-time actionable insights generated by data analytics such as waste reduction, anomaly detection, asset utilization, and downtime can help you gauge operational performance accurately. These insights can then be used to take informed business decisions, which drive growth.
- Enhance collaboration: Although manufacturers collect data traditionally as part of their operations, the data is siloed and only available to either operational or IT teams. A smart manufacturing platform can provide a more holistic picture: it generates data insights including real-time performance and desired benchmarks, which can be shared across the entire organization to drive process improvements.
- Enable predictive maintenance: Data can be used to deploy machine learning models that lead to higher quality products and predictive maintenance. Machine learning capabilities can be used to predict and prevent disturbances before they impact operations.
- Boost workplace morale and productivity: Smart manufacturing brings along with it, the ability to manage devices and access data remotely. Remote operations empower employees tremendously, resulting in more flexibility, quality, and efficiency.
In a nutshell
Many companies, which have embarked on the digital transformation journey, still don’t have a fully connected shop floor sending useful data across the enterprise. Many manufacturers have made the unfortunate mistake of lopping in smart manufacturing initiatives with larger and more complex IoT initiatives.
They are quite hesitant to invest in new technologies, owing to the current economic scenario. However, manufacturers have to invest in digital transformation to keep pace with rapidly evolving market demand and stay relevant.
Data is already likely available in heaps: computers are present at every point in the manufacturing enterprise, sensors are pervasive on the shop floor, and across the supply chain. You simply need to put the technology in place to tap into this data effectively and unlock valuable insights.
Ask yourself this question: what does my enterprise need to become more agile? The list probably includes connected assets, a unified technology platform to collect all the data in one place, process and analyze it. Lastly, you need the ability to share that data seamlessly with all stakeholders.
So, what are you waiting for? Start by getting both your IT and OT stakeholders on board and agree upon the end goal for a smart manufacturing initiative. Then, deploy and leverage a factory with connected assets to mine intelligent data insights and share it across the enterprise.
Today, the need for smart manufacturing is more critical than ever before: it can help you enhance the quality of your processes, eliminate bottlenecks, and tweak production levels to meet market demand accurately. If you’re looking for a custom smart manufacturing solution, talk to Hakuna Matata’s team of experts and find out how we can help!
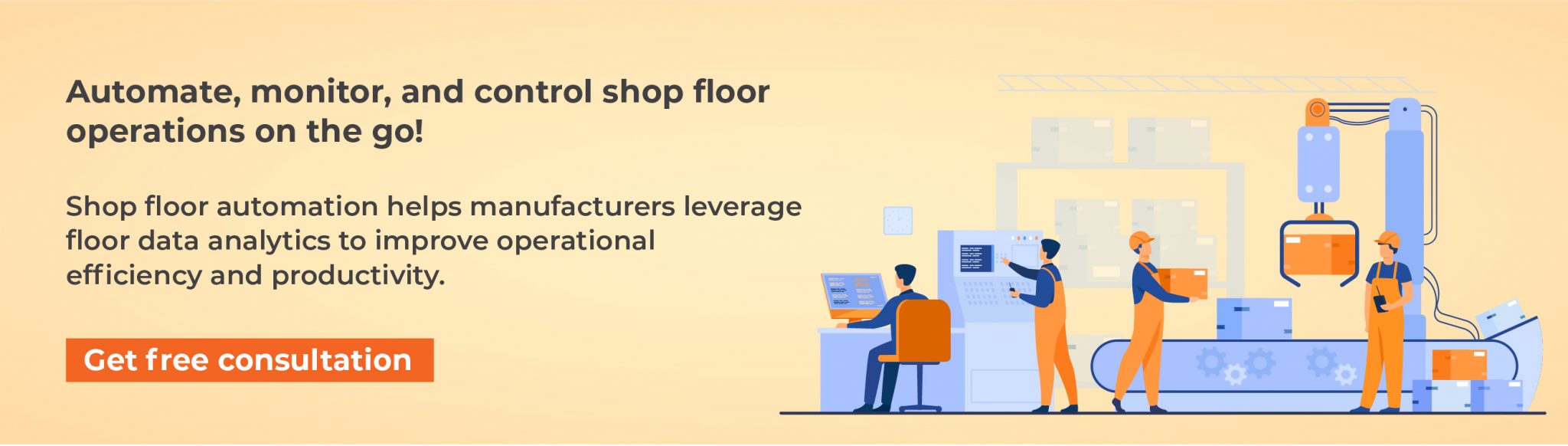