4 Reasons Why Asset Tracking Solution Will Help Your Construction Company
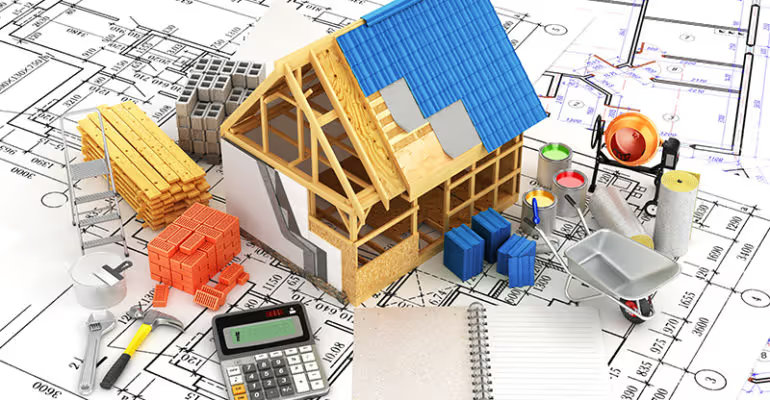
Tracking and managing assets efficiently is the biggest concern for any construction company. Most often, construction employees/supervisors will have no clue or control over assets and this costs them dearer.
Wait, it’s not over. Besides the cost, the entire project will come to a standstill (provided you don’t partner with an experienced IoT app development company) resulting in a greater loss compared to the cost of repairing the equipment or even buying a new piece!
This is one of the reasons why most construction companies have started to adopt cutting-edge techno-enabled digital solutions from reliable digital transformation services to mobilize their asset tracking and management processes to reduce asset costs and improve the project’s success rate.
According to a report from marketsandmarkets, the asset management system market size is expected to soar across Asia-Pacific (especially), and all over the globe.
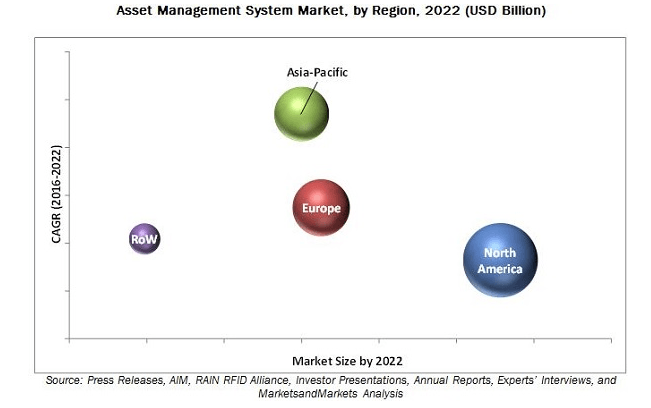
From the above statistics, it’s prudent that asset tracking and management systems are widely used by companies as they simplify material movements.
The sections below will help you understand how an asset tracking and management system will simplify the complex material movement tracking process and optimize project performance.
Tracking assets is a must for all industries and has been in vogue since the beginning of the industrial revolution. It is about maintaining an inventory of all the physical assets, including not only equipment & materials but also employees.
SEE ALSO: "Asset Tracking & Management with IoT"
What we are seeing in the age of Industry 4.0 is a whole new dimension. The technology advancements have helped construction companies to bolster their asset tracking processes and save cost. Below are a few ways construction companies are using technology solutions.
(1) Digital tracking of physical assets using barcodes, identification tags like RFID, QR-code to identify and locate each asset inside a project zone and track its information, maintenance requirements for utilizing it to the fullest.
(2) Gathering and analyzing data on the use of the equipment and generating insights and alerts to help inefficiency.
Which is why, today, construction companies, equipment leasing firms and equipment manufacturers are eyeing significant benefits in the digital transformation of asset tracking and management, be it tools or generators or heavy machinery.
Here are 4 must-know reasons why construction companies are opting for digital asset management systems and how they are accelerating the construction project.
1. Efficiency: The obvious priority
From streamlining daily operations to protecting equipment, digital tracking enables easy monitoring of asset safety and use.
Tracking assets offers a clear picture of how materials are being used. Having on-time information on surplus at any given time provides insight into the management of supply and helps perform a balancing act when it comes to stock.
Whether having backup resources or cutting down on stocking of unnecessary resources, knowing exactly how much you use can help you make smart decisions and avoid cost overruns. Asset tracking informs us of how long equipment lasts, and factor in replacement costs.
2. Productivity: The everyday imperative
Asset tracking increases productivity by drastically reducing the time spent looking for equipment, recovering from unexpected malfunctions, and maximizing the efforts. The malfunctioning of a single piece of equipment can cause the loss of productive work for several days.
You can maintain high levels of productivity by knowing exactly when and how your equipment is being used, and thereby have on-time information on required and preventative maintenance. This means minimal equipment breakdowns that result in downtime.
Accurate paperless inspections can make sure that equipment is in peak condition, which not only improves productivity and efficiency but also enhances on-the-floor safety.
3. Data and analytics: Utilizing assets to the fullest
Construction companies own and operate a huge number of assets. Using a smart asset tracking system they can consolidate and centralize data from all of their assets. Such data can point construction teams to equipment issues before they become threats.
With the centralization of construction asset data in one place, organizations can track their utilization better and take steps to improve it. Access to utilization reports helps construction equipment managers understand which equipment is being used how, across locations, and make informed decisions regarding the purchase or renting or movement of equipment.
Utilization reports also show run time of every piece of equipment, which can be used to match with reports of work accomplished to identify discrepancies.
4. Better utilization of human resources: The game-changer
The new-age asset tracking has one significant benefit that simply has the potential to make the construction industry climb the value chain. With smart asset tracking, all the personnel at the construction site have the right information at their fingertips, enabling better collaboration. Organizations can share important asset records with relevant personnel to reduce redundancy and improve efficiency.
With smart devices and software systems doing the job of asset tracking and delivering alerts and insights to enable preventive maintenance, the employees can focus their energies on their core function – construction.
By now, you’d have realized why asset management matters for your company and how it will improve your project at reduced asset costs.
Struggling with your existing asset management system? Let’s talk.