Complete Guide to Calculating & Improving Overall Equipment Effectiveness (OEE)

Guide to Calculating and Improving Manufacturing OEE
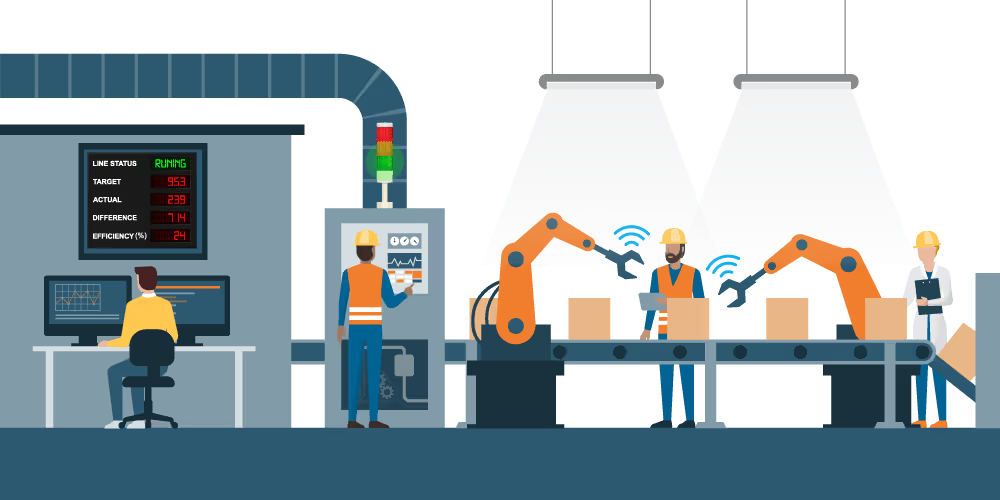
Why should you measure OEE data – to identify the reasons for downtime and improving the equipment effectiveness to streamline and accelerate production rate.
Don’t know how to calculate your OEE value? Don’t worry. You’re not alone.
The purpose of this guide is to help everyone understand everything about OEE and ways to improve it.
- What is OEE
- Why OEE
- Efficiency vs. Effectiveness
- OEE benchmarks
- OEE benefits
- How to calculate OEE
- How to improve OEE
- OEE case study
Let’s get started with OEE
What is OEE?
Overall equipment effectiveness is a key KPI (includes a combination of a few key parameters) for real-time production monitoring and measuring. It is always calculated in percentage.
Practical definition to OEE
OEE (Overall Equipment Effectiveness) is the Gold standard for measuring manufacturing productivity and efficiency.
Simply put – it identifies the percentage of manufacturing time that is truly productive.
An OEE score of 100% means you are manufacturing only Good Parts, as fast as possible, with no Stop Time. In the language of OEE that means 100% Quality (only Good Parts), 100% Performance (as fast as possible), and 100% Availability (no Stop Time). (source: oee.com)
Why OEE as an important KPI for manufacturing success
OEE is a key KPI for efficiency tracking. The data provides complete details about productivity rate, which in turn helps in reducing downtime, waste etc.
While we have other KPIs like Overall Operations Effectiveness (OOE), Total Equipment Effective Performance (TEEP), measuring OEE is the most focused and measured KPI because it plays a critical role in identifying root cause issues and accelerating the productivity and RoI.
OEE benchmarks
While setting OEE as a KPI for measuring equipment effectiveness is a great move but what do you measure against. You need a baseline right? This is where the OEE benchmark comes in.
- An OEE score of 100% stands for perfect production.
- An OEE score of 85% is considered as a world-class benchmark for discrete manufacturers with a little room for improvement.
- An OEE score of 60% is for discrete manufacturers means there is some room for improvement.
- An OEE score of 40% is quite common among manufacturing companies that just start tracking and improving manufacturing performance. It is a low score and should be addressed quickly.
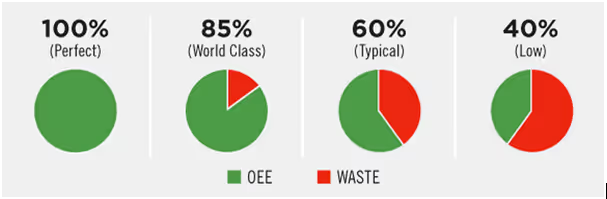
How to calculate OEE and factors contributing to it
As far as OEE is concerned, there are 3 factors that contribute to the OEE data: Availability, Performance and Quality.
OEE = Availability x Performance x Quality
How to calculate OEE – includes formula with examples
Let’s dive deep into each factor in the sections below and let us find out how they are calculated.
What is Availability in OEE
It is all about the availability of the machine during a planned schedule. Availability of the machine helps in identifying the losses whenever there is a STOP time or changeover.
The STOP time can be planned or unplanned or changeover, it can impact the availability of the machine leading to produce less than expected.
While changeovers can’t be eliminated completely, reducing them is always viable to reduce availability loss.
Availability is calculated as shown below.
- Produced in right time – availability
Availability (%) = Run Time (operating time) /Net available time
*Operating Time = Net Available Time – Unplanned Downtime
* Net Available Time = Shift Length – Planned Downtime
What is Performance in OEE
Performance in OEE provides data on the speed which the machine performs against the desired speed. While the ideal machine running time may be of a certain capacity, real-time running time might be relatively slower.
This can be due to minor stops, idle time or reduced speed.
Addressing these challenges will help improve the speed on the work centre and reduce performance loss.
This is how Performance is calculated.
- Producing product within a stipulated time – Performance
Performance = (Ideal Cycle Time × Total Count) / Run Time
What is Quality in OEE
Quality in OEE represents the number of goods produced without any defect. If you’ve 100% of goods produced without any defect, then the work centre is performing phenomenally. However, this rarely happens. It is all about reducing the defective products and producing only good quality ones.
This is how Quality is calculated.
- Produced in right way – Quality
Quality(%) = (Total Parts Produced – Total Scrap) / Total Parts Produced
OEE Calculation Example
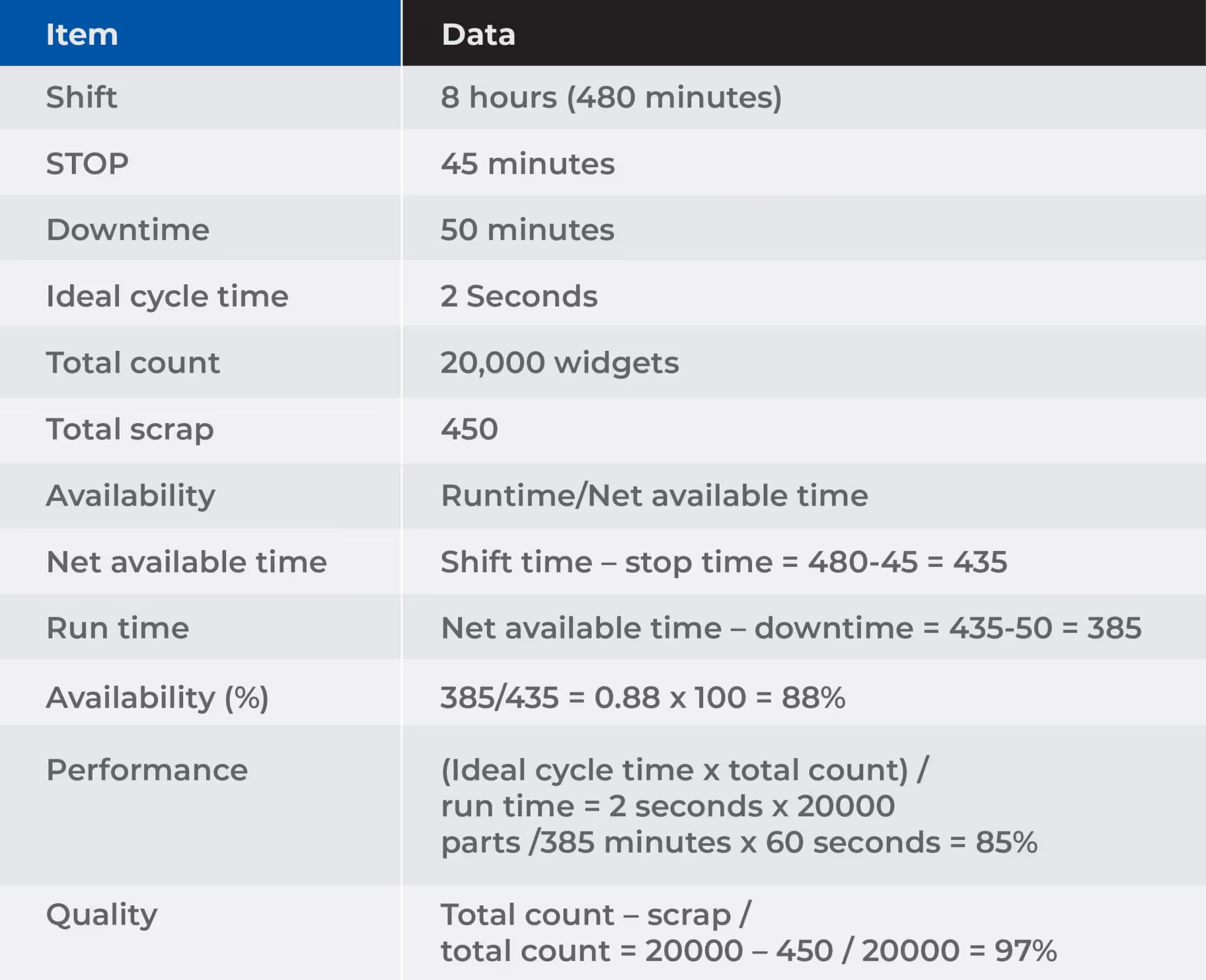
How to improve OEE Using IoT, mobile app, predictive maintenance
OEE Automation Software
An industrial IoT application coupled with a strong predictive maintenance system can improve overall equipment effectiveness by at least 10x.
Availability – Capturing and tracking real-time machine efficiency using IoT (for manufacturing) helps in meeting the targets expected for machines and humans involved in the process.
Performance – The IoT data collected from machine and human operations helps identify the frequent downtime and plan for reducing STOP times.
Quality – Thought Quality can’t be improved directly through such a system, it can be achieved by improving the Availability and Performance of the process.
This is how the system works.
IoT – the IoT devices (with sensors) would be fixed on the machines and its real-time downtime and performance under different conditions is captured and pushed to mobile data and to the cloud IoT Platform.
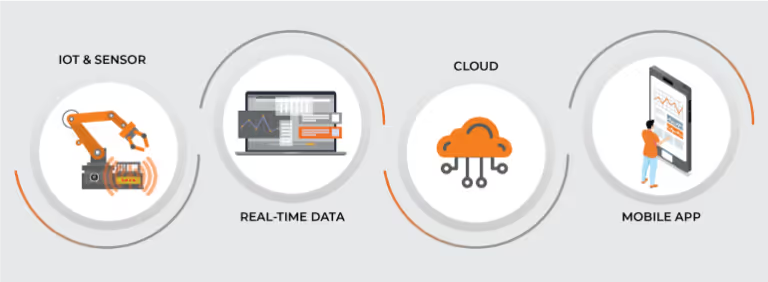
The data captured is then fed into the AI and ML-based predictive maintenance system to predict unplanned downtimes in the future. The entire system provides a massive volume of real-time data that helps in improving the OEE at the work centre.
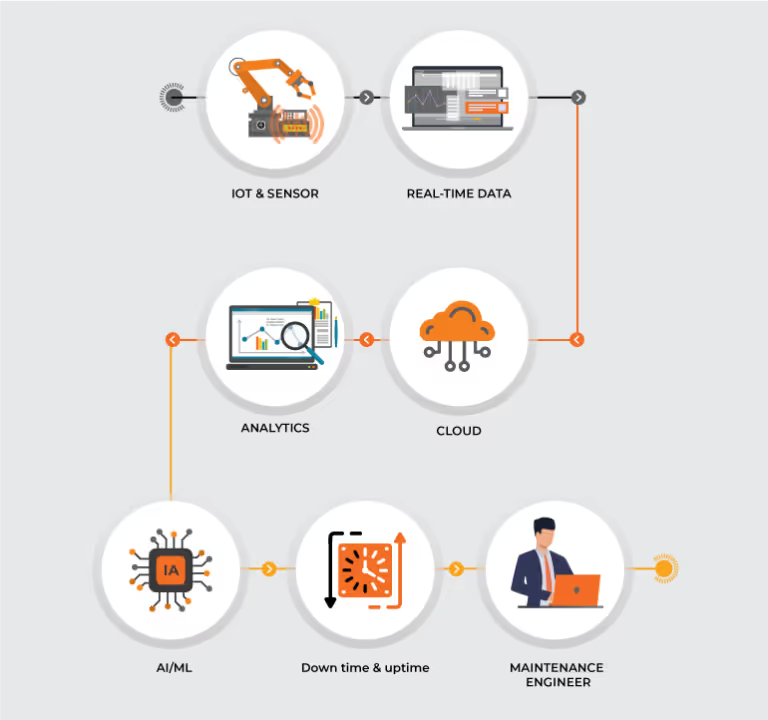
Effectiveness vs. efficiency – What to measure
A short comparison would be:
- Effectiveness – the rate of what is expected with respect to what is produced
- Efficiency – Maximum performance of machines under different conditions.
The debate between effectiveness and efficiency is always on and many still presume that both mean the same. However, effectiveness is all about how much can be produced with respect to what is expected and depends on required raw materials, machine availability and other resources.
On the other hand, efficiency is all about how much the machine itself can produce to its capacity under different conditions.
In short, a 100% efficient machine is one of the factors that will improve effectiveness on the manufacturing floor.
OEE benefits
- All-in-one metric for measuring manufacturing productivity
- Helps map production efficiency with reporting
- Maximize equipment RoI
- Improve quality
Measurement of OEE for a Leading Manufacturing Company
Our client is leading Industrial Packaging manufacturer supplies to some of the major oil distributors in the region. One of the key challenges they are facing is they were running additional shifts with overtime to meet the production demands. But the production demands were well within the production capacity of the plant. Identifying the reasons for inefficiency and bringing in transparency to all the stakeholders were the expected output of the projects.
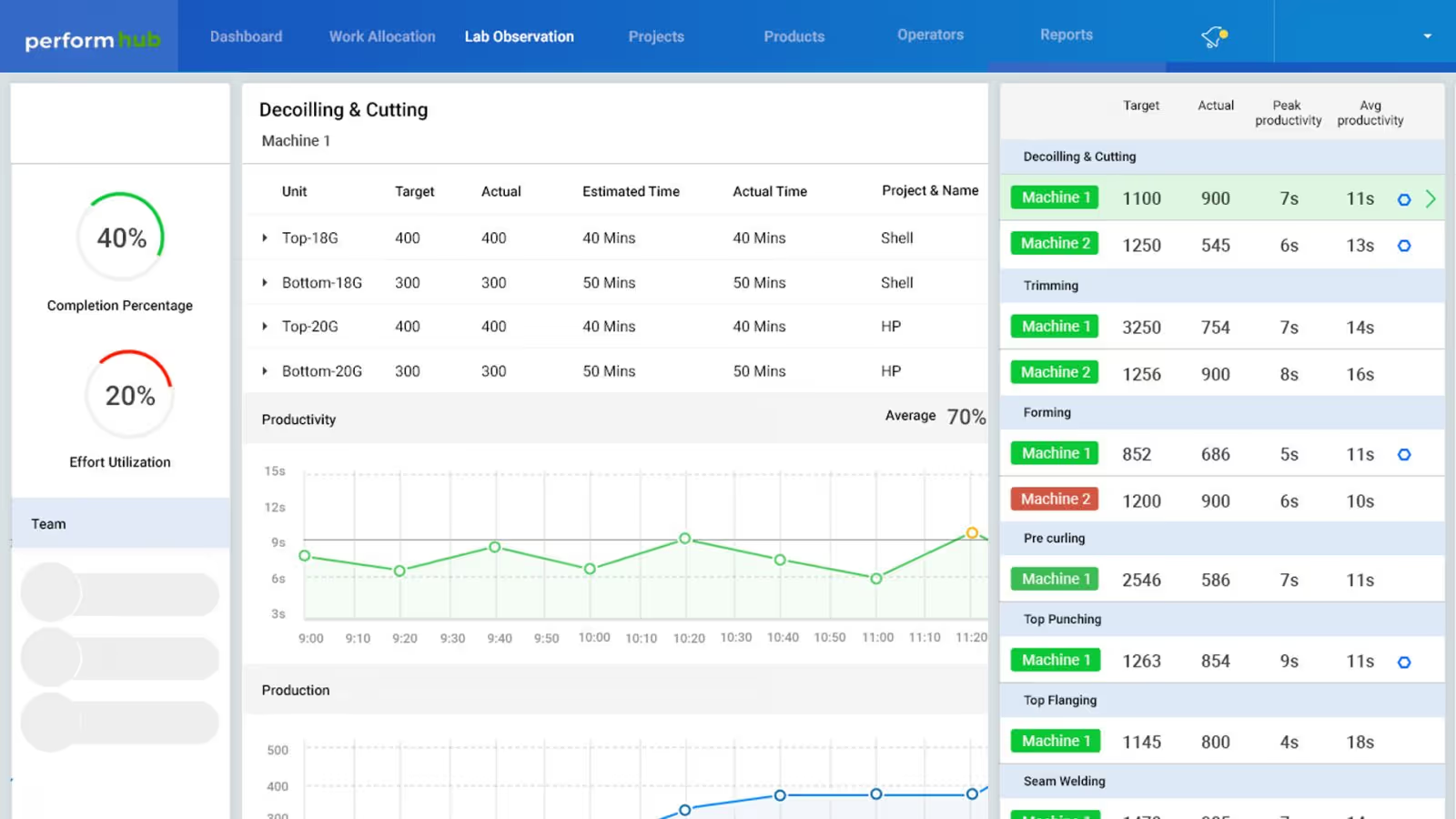
The shop floor – assembly line had seven stages and two variants of the products were produced on any given day. Measuring the productivity at each stage in real-time both machine & labour was the key piece of the puzzle.
Additionally, the machine downtime has to be captured and notified to the shop floor supervisor to act promptly and reduce the impact to ensure operations are back on track. Having real-time machine productivity data enabled the supervisors to rectify the problems instantly rather than waiting for a mishap to happen.
We implemented the connected factory solution by fixing sensors at each stage to measure the output and detect the downtime of the machines. The sensors are connected to the IoT hub, which in turn sends the data to an “IoT Platform”, on top of which an analytics engine was built.
We digitized the shop floor operations management right from operator allocation, product change over to measuring labour & machine productivity (OEE & LE) through Industry 4.0 solution.
With access to data on-the-go (Mobile & Web Dashboards), clients were able to identify the bottlenecks and rectify them to improve productivity by 20%. The transparency was created for shop-floor operators by TV displays in the shop floor which in turn helped in increased productivity.
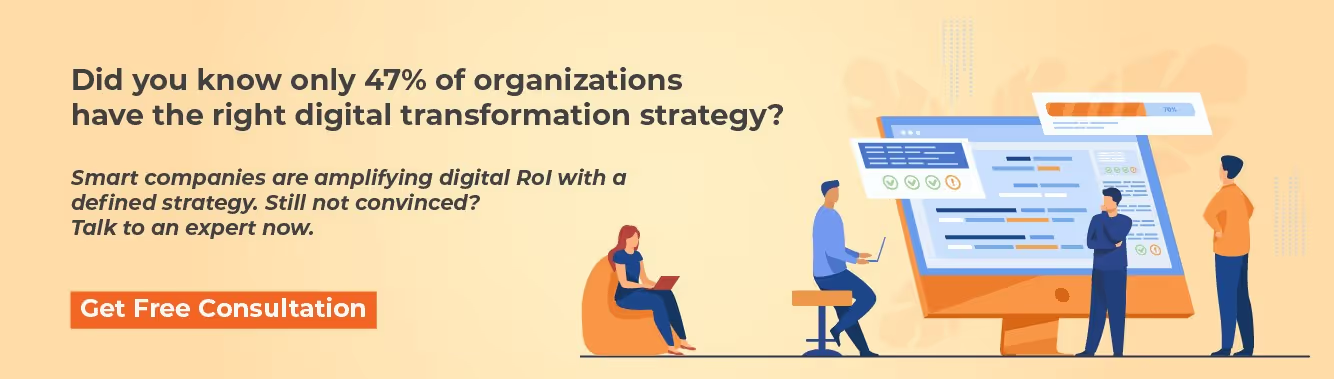