Minimize Manufacturing Scrap: Boost Profits & Efficiency
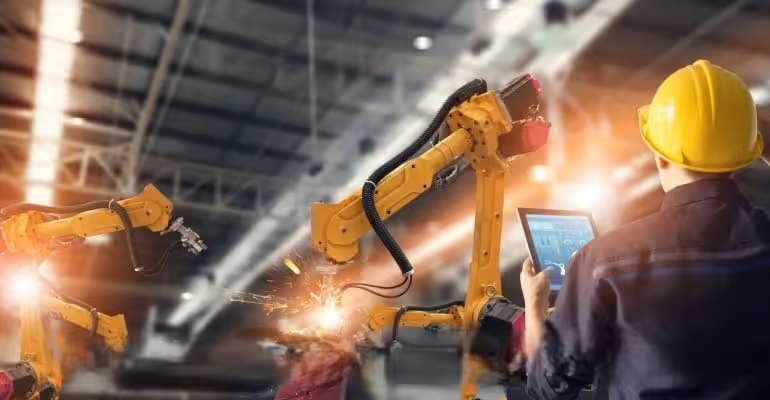
How I Cut Manufacturing Scrap by 40% Using IoT: A Developer's Real Experience
I've spent eight years building IoT solutions for manufacturers, from Detroit auto plants to Taiwan chip fabs. I've watched sensors and smart systems transform production lines and save millions in wasted materials.
Today I'll show you exactly how I help manufacturers cut scrap by 30-50% in their first year. These aren't theories, these are real results from real factories.
Quick Facts About Manufacturing Scrap
What Creates Manufacturing Scrap (And How Much It Really Costs)
Let me tell you about a powder coating plant I worked with three years ago. The plant manager showed me barrels of contaminated powder, thousands of dollars worth, that they threw away every time they switched paint colours.
"We're literally dumping money in the trash," he said.
I see this everywhere. Scrap comes from many sources, and most manufacturers only know about the obvious ones.
At that powder coating plant, I installed sensors that watched powder flow rates, booth pressure, and electrostatic charge in real-time. We cut their transition waste by 60% in six months. We used actual data instead of guesswork to time their changeovers perfectly.
The True Cost of Scrap: It's Worse Than You Think
Most manufacturers only see the tip of the iceberg. I worked with a precision machining shop that made aerospace parts. They thought scrap cost them $50,000 per month—just the titanium they threw away.
After I installed IoT monitoring on their CNC machines, we found the real cost was $200,000 monthly.Here's the breakdown:
My IoT system paid for itself in three months. We caught calibration problems before they made bad parts.
In semiconductor manufacturing, I've seen single wafers worth $10,000 or more. When I helped one fab implement predictive maintenance, we prevented equipment failures that would have scrapped entire lots. We saved millions in one quarter.
How IoT Cuts Scrap: My Proven System
I've developed a system that works. I focus on three key areas that deliver the biggest scrap reductions.
Stage 1: Real-Time Monitoring - The Foundation
I start every project with sensors at critical points.
Here's my standard sensor package:
I connect these sensors to PLCs and SCADA systems that make immediate adjustments. Too many "IoT" projects just collect data without taking action.
Stage 2: Predictive Maintenance - Stop Problems Before They Start
Last year, I put predictive systems in a paper mill. We watched bearing temperatures, roller pressures, and web tension across their line. The system learned normal patterns and could predict bearing failures two weeks early.
Before IoT: Monthly bearing failures, 4-6 hours downtime each, thousands of feet of scrapped paper
After IoT: Zero unexpected failures in year one, virtually no bearing-related scrap
Stage 3: Process Optimization - Find the Sweet Spots
I worked with a food plant that scrapped 8% of production due to inconsistent quality. I installed sensors throughout their mixing, cooking, and packaging processes.
We found that tiny changes in mixing speed and temperature changes operators couldn't detect, caused most quality problems. By automatically adjusting these parameters based on sensor feedback, we cut scrap to under 2%.
The Real Challenges: What They Don't Tell You
I've hit every obstacle in the book. Here's what you'll face and how to handle it.
My Approach to Overcoming Obstacles
Start Small, Win Big: I always begin with the highest-value processes. Small improvements in critical areas generate big financial returns. Use those wins to fund expansion.
Fight Data Overload: I focus ruthlessly on actionable insights. Every sensor must answer a specific question: "Will this data help us prevent scrap?" If not, we don't install it.
Plan for Integration Hell: Manufacturing plants mix equipment from different decades. Getting modern sensors to talk to 1990s PLCs while connecting to cloud platforms takes time. I budget 30-40% of project time just for integration.
My 4 Best Practices That Always Work
These strategies deliver results every time. I use them in every project.
Practice 1: Document Everything During Changeovers
I start every project by watching changeover processes. Most plants have tribal knowledge about the "right way" to switch products, but it's rarely documented.
At that powder coating plant, different operators used completely different changeover sequences. Some were efficient, others wasteful. By capturing sensor data during changeovers and matching it with scrap levels, we found the optimal procedures and automated them.
Results: 60% reduction in changeover waste, 40% faster changeover times
Practice 2: Set Up Quality Gates Early in the Process
Catch defects early, before you add more value. I've had great success with in-line inspection systems that use computer vision and sensors to check quality at multiple process points.
At one electronics plant, we installed vision systems after each major assembly step. Instead of finding defects only at final testing (after adding all components), we caught problems immediately and could often rework parts instead of scrapping them.
Practice 3: Track Leading Indicators, Not Just Lagging Ones
Most manufacturers only track scrap rates, a lagging indicator that tells you about problems after they cost you money. I focus on leading indicators that predict scrap before it happens.
Leading vs Lagging Indicators for Scrap Prevention
Practice 4: Create Closed-Loop Control Systems
The most powerful IoT systems don't just monitor—they automatically adjust processes to maintain optimal conditions.
Automated Control Applications That Cut Scrap
I've built systems that:
- Automatically adjust mixing speeds based on viscosity measurements
- Modify curing temperatures and times based on material properties
- Change cutting speeds when tool wear sensors detect degradation
These systems respond in seconds, not hours or days like human operators.
Real Success Stories: The Numbers Don't Lie
Here are three recent projects that show what's possible when you do IoT right.
Case Study 1: Automotive Stamping Plant
The Problem: High scrap during die changes, 12% scrap rate due to inconsistent part dimensions
My Solution:
- Installed load cells on the press
- Added position sensors on the die
- Automated the die setup process
- System automatically adjusts press tonnage, shut height, and timing
The Results:
Case Study 2: Chemical Processing Facility
The Problem: Batch-to-batch variation causing 15% of products to fail quality specs
My Solution:
- Deployed wireless sensors in reactor vessels
- Monitored temperature, pressure, pH, and mixing energy
- Used machine learning to predict optimal reaction conditions
The Results:
Case Study 3: Electronics Assembly Line
The Problem: Component placement errors causing high rework rates and customer returns
My Solution:
- Implemented vision-guided robotics
- Added real-time quality feedback
- Each placement verified immediately with automatic correction
The Results:
Industry Benchmarks: How My Clients Compare
What These Success Stories Teach Us
- Start with your biggest pain point: All three companies focused first on their highest-cost scrap sources.
- Automate the response: Manual monitoring isn't enough, systems must respond automatically
- Measure everything: You can't improve what you don't measure precisely
- Think beyond materials: Factor in all costs, labour, machine time, customer impact
What's Coming Next in IoT Manufacturing
I talk to technology vendors and visit trade shows constantly. Here's what I see coming that will make scrap reduction even better.
Emerging Technologies for Scrap Reduction
Edge AI: More sophisticated machine learning running directly on plant hardware. This means faster response times and less dependence on cloud connections. I'm already testing systems that can detect quality problems in milliseconds, not seconds.
Digital Twins: Virtual models of production processes that simulate different scenarios. You can test changes before applying them to real equipment. I expect this to cut development time for new processes by 60%.
5G Connectivity: Ultra-low latency wireless that enables real-time control applications. Currently, critical control loops need wired connections. 5G will change that.
Augmented Reality: AR systems that overlay IoT data directly onto equipment. Operators can see what sensors detect and understand why systems make adjustments. This reduces training time and improves troubleshooting.
Investment Priorities for 2025-2027
Based on my client conversations, here's where manufacturers plan to spend:
The Conversation We Should Have
If this story resonates with you, if you see your operation in these examples, then we should talk. Not because I want to sell you something, but because I want to understand your biggest waste challenges.
Maybe it's setup waste during product changeovers. Maybe it's quality issues that create expensive rework. Maybe it's equipment failures that scrap entire batches.
Whatever it is, I guarantee it's costing you more than you think. And I guarantee there's a way to fix it that will pay for itself faster than you expect.
The manufacturers I work with don't just reduce scrap, they sleep better, stress less, and build more profitable businesses. Their employees take pride in their work because they're not constantly fighting preventable problems.
Their customers trust them because quality is consistent. Their competitors wonder how they're able to bid so aggressively while maintaining margins.
That could be your story.
But first, you have to decide: are you going to keep throwing money in the dumpster, or are you ready to keep it in your bank account where it belongs?
The choice is yours. But choose quickly, your competitors already are.